The Hadza people, who live in remote areas, produce iron arrowheads themselves. Contrary to what is often mentioned in the literature, they do not buy these iron arrowheads from the Datoga people. Both tribes used different production methods. Whereas the Hadzabe people cold-forge the iron arrowheads from nails, the Datoga hot-forge metal scrap.
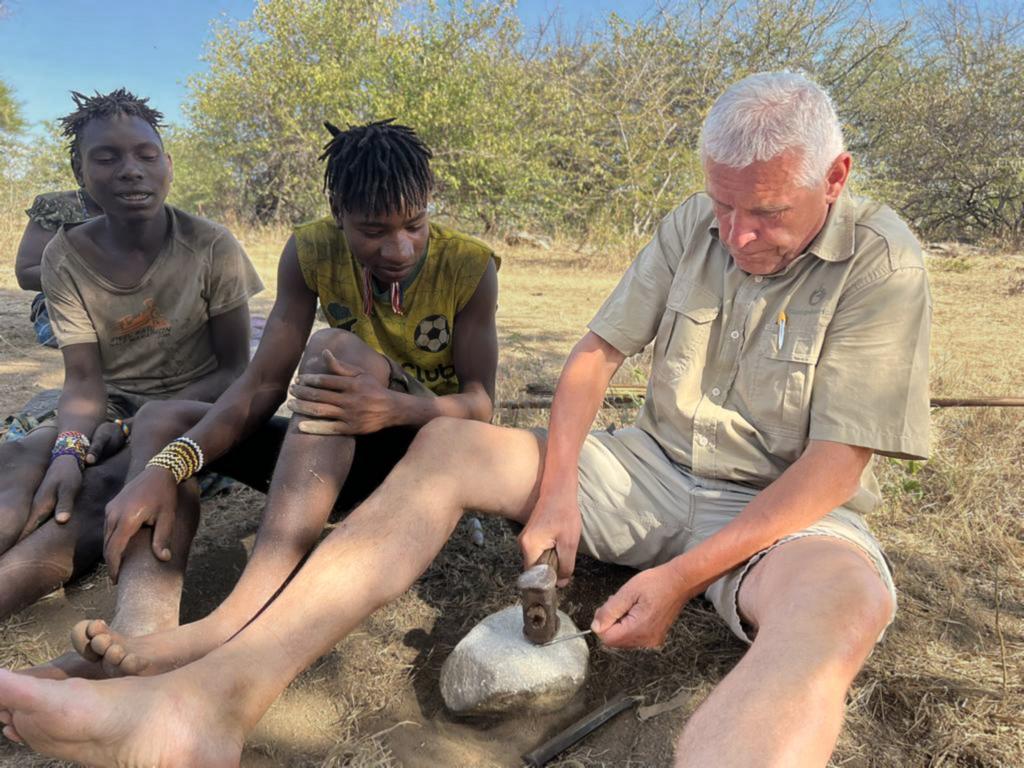
Source material used for iron arrowheads
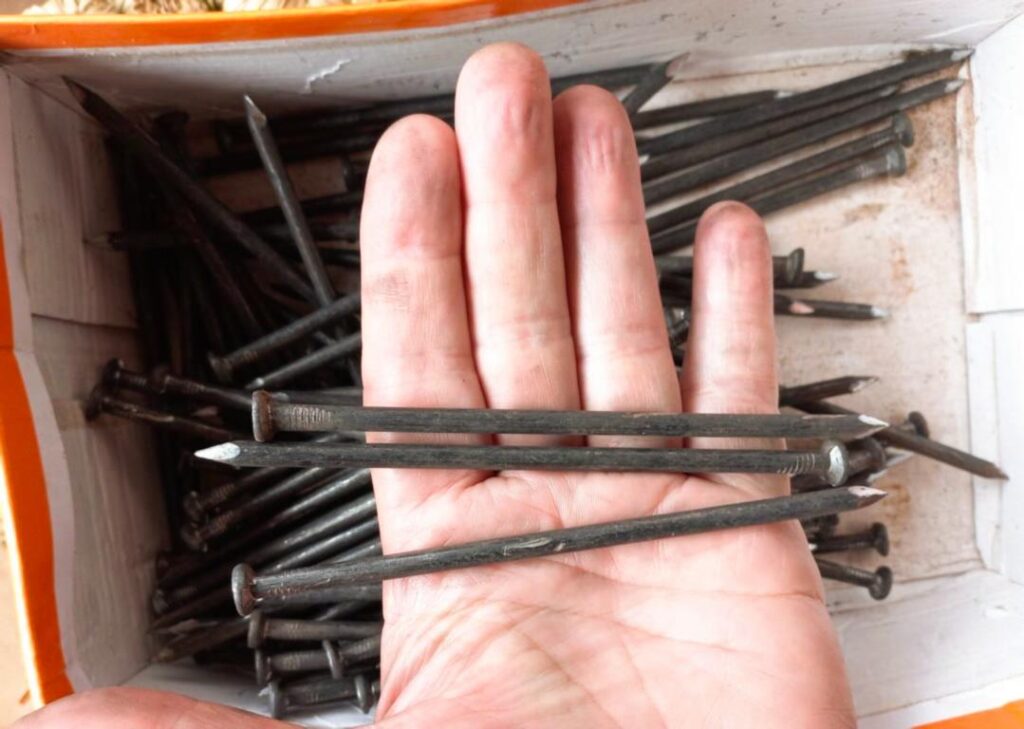
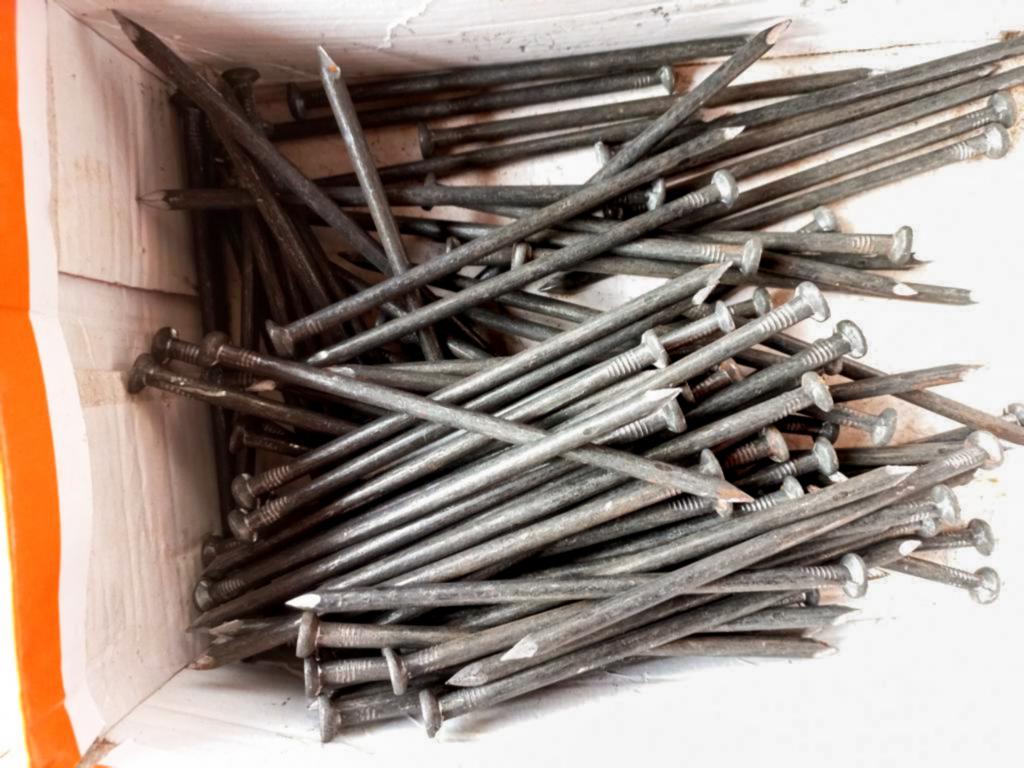
As explained in one of my former articles here, the Hadzabe people use two basic shapes of iron arrowheads: a lance-shaped blade and a barbed arrowhead. The same source material is used for both basic shapes: heavy framing nails. These nails are 4-1/2’’ (30d) / 11.4cm long, and their shank is 0.22’’ / 5.6mm thick.
Tools used for forging
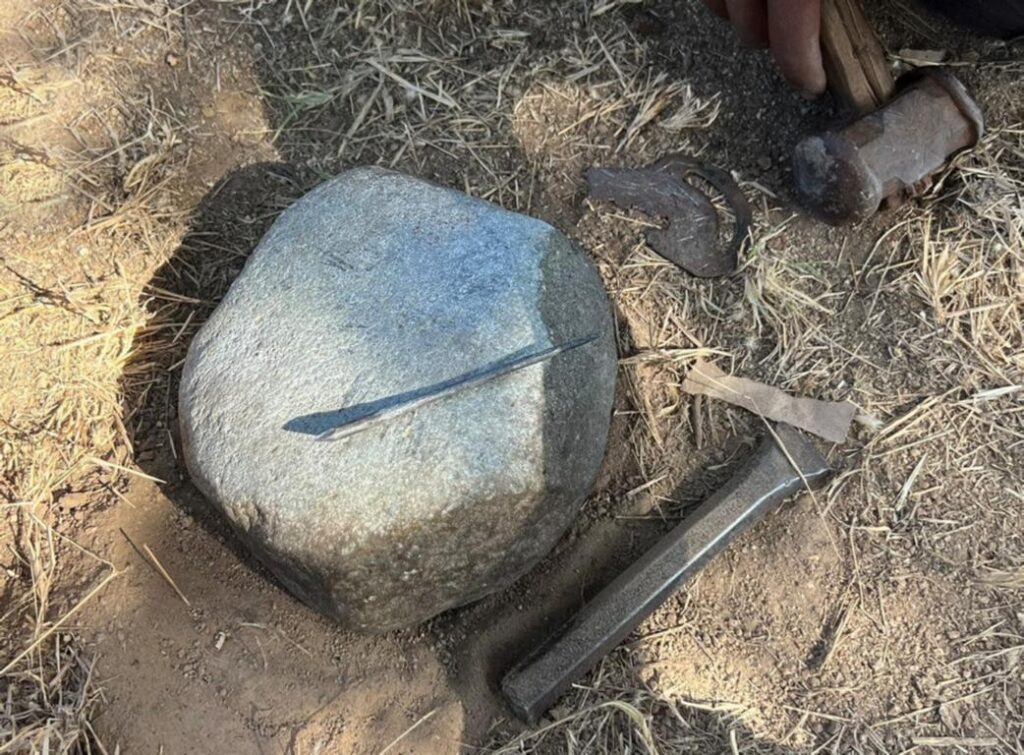
The nails are hammered into shape on a field stone anvil with a metal hammer. The Hadzabe clan we met only had one piece of a very old iron hammer and always used the same stone for cold forging as an anvil. They used a cold chisel and a piece of flat, oddly shaped scrap metal plate to trim the crudely forged blades into the required shapes.
The forging was done in three steps, each by a different person. Hadza A hammered the nails into two separate spikes. Hadza B forged a crude, barbed broadhead onto one end of each spike, and Hadza C finished the arrowheads. We will discuss these steps in more detail in the following.
1st step of cold-forging
Initially, a 30d framing nail will be hammered into a long, thin, and square shape. Due to the primitive cold-forging on the stone anvil with the half-round hammerhead, this thin metal stick is finally shaped like an animal’s horn.
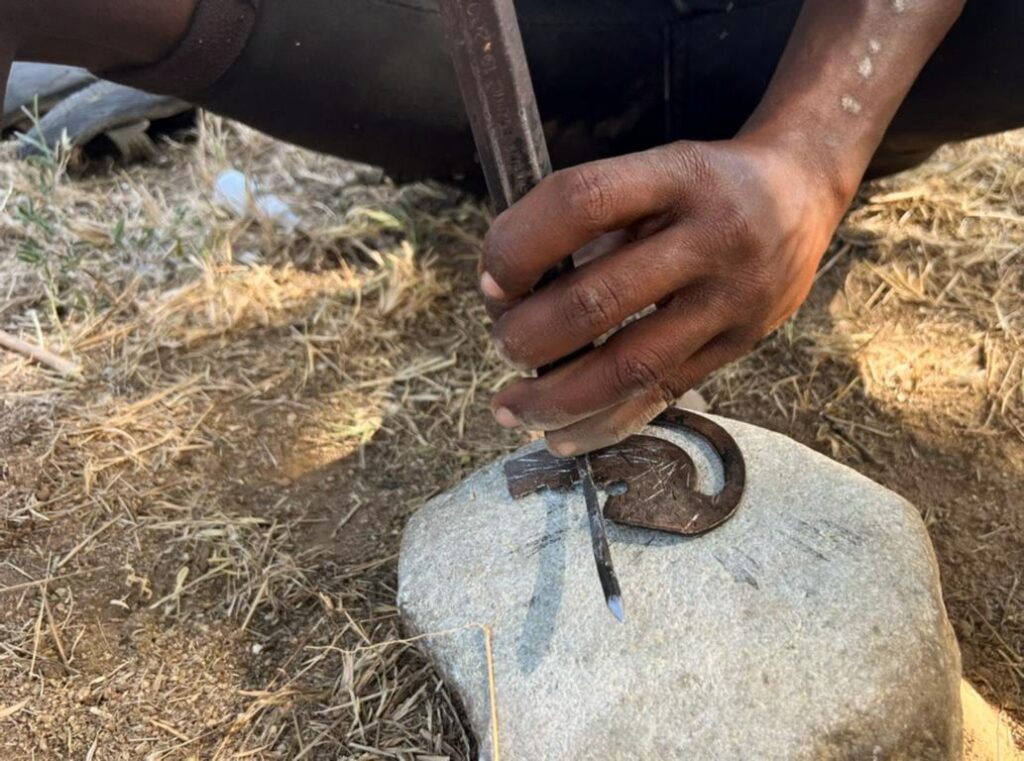
The initially formed metal stick is cut in half with the cold chisel, resulting in two metal sticks for future iron arrowheads.
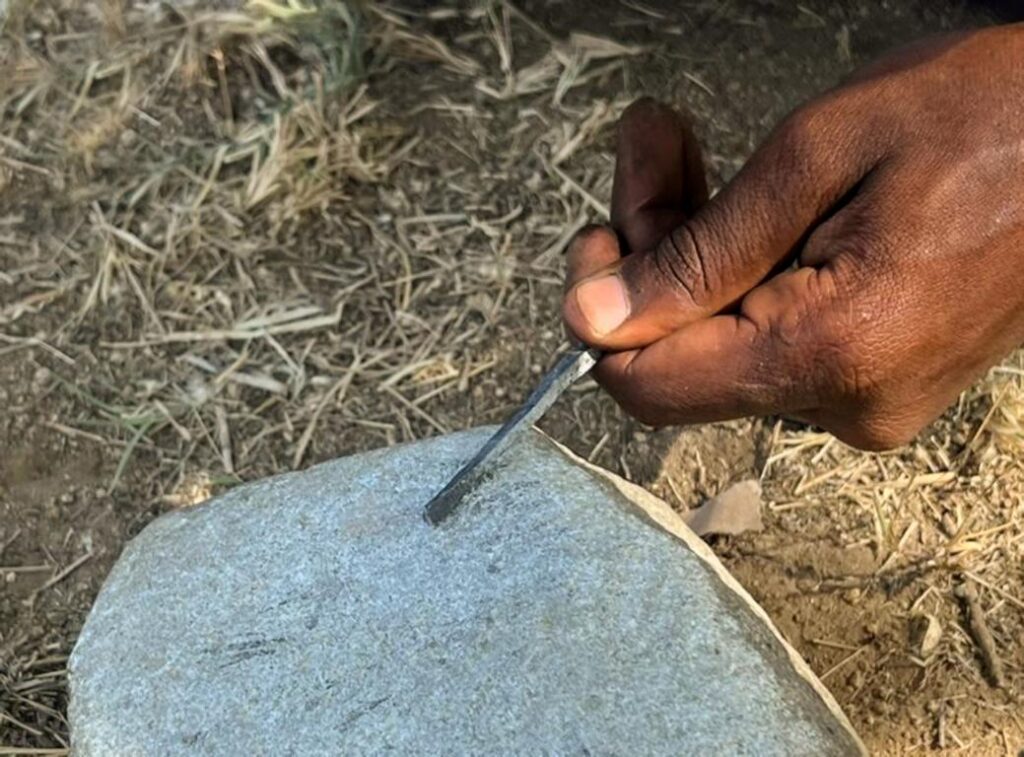
Each square metal stick is now hammered into a round, conical shape. The slim, conical end will be the shank of the arrowhead fitted into the arrow shaft.
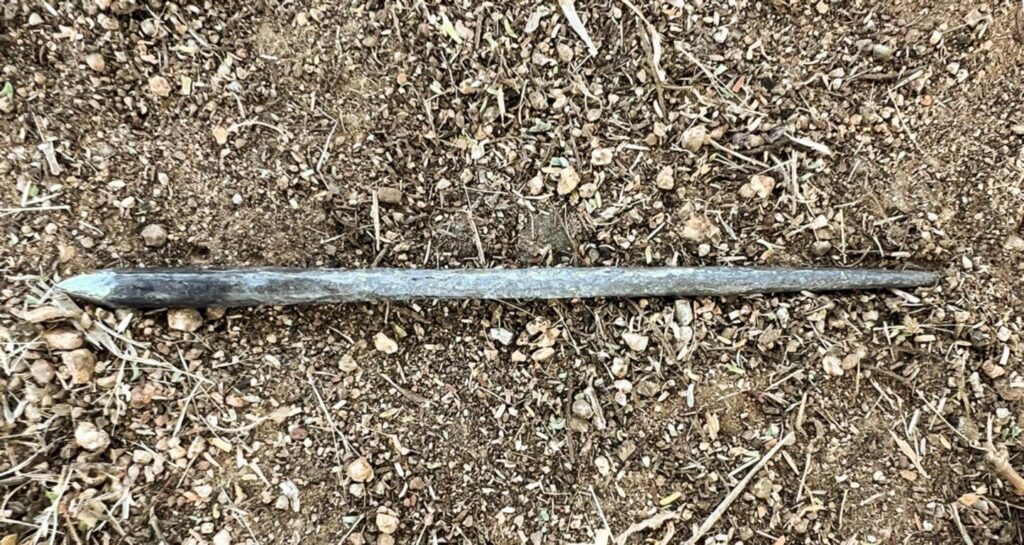
The metal stick’s thicker end will be turned into the future broadhead during the next steps.
2nd step of cold-forging
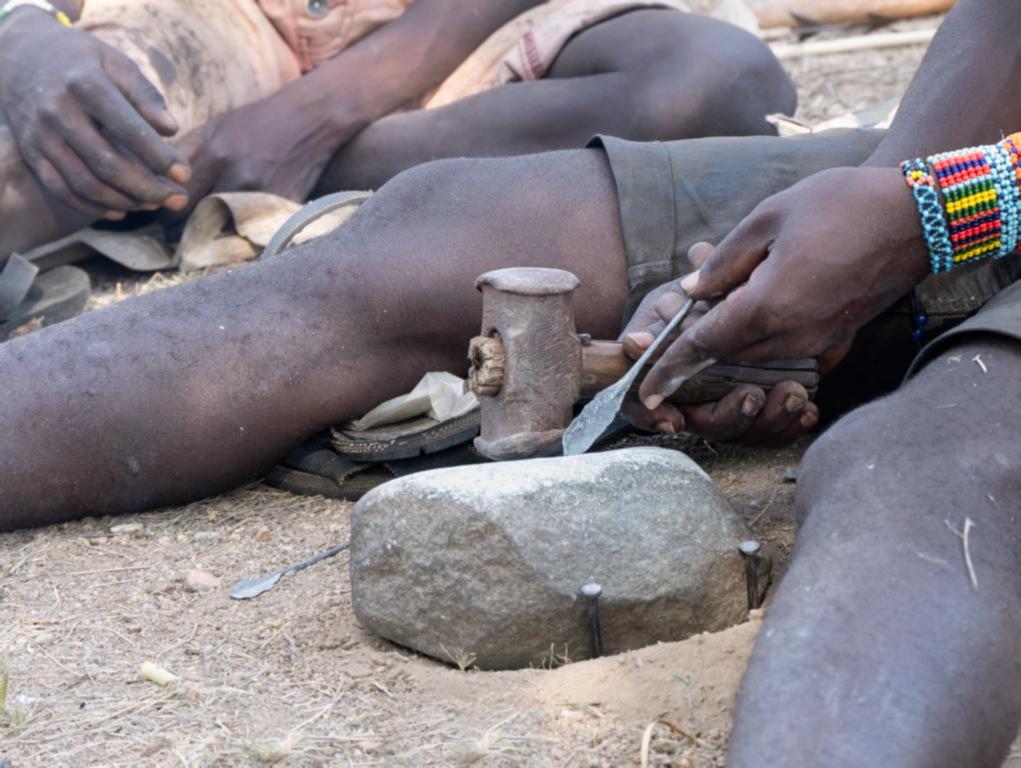
Now, the next Hadza man is taking over the cold forging, broadening the thick end of the metal stick. During flattening, special care is needed to shape the future tip into a continuous thickness.
After flattening the head, the rough shape of the future broadhead will be chiseled out, and the roughly forged iron arrowhead will be handed over to the next Hadza man for the final shaping.
3rd step of cold-forging
The most experienced hunter performs the third step of producing Hadzabe arrowheads. First, he hammers the arrowhead into the flat shape that is finally needed.
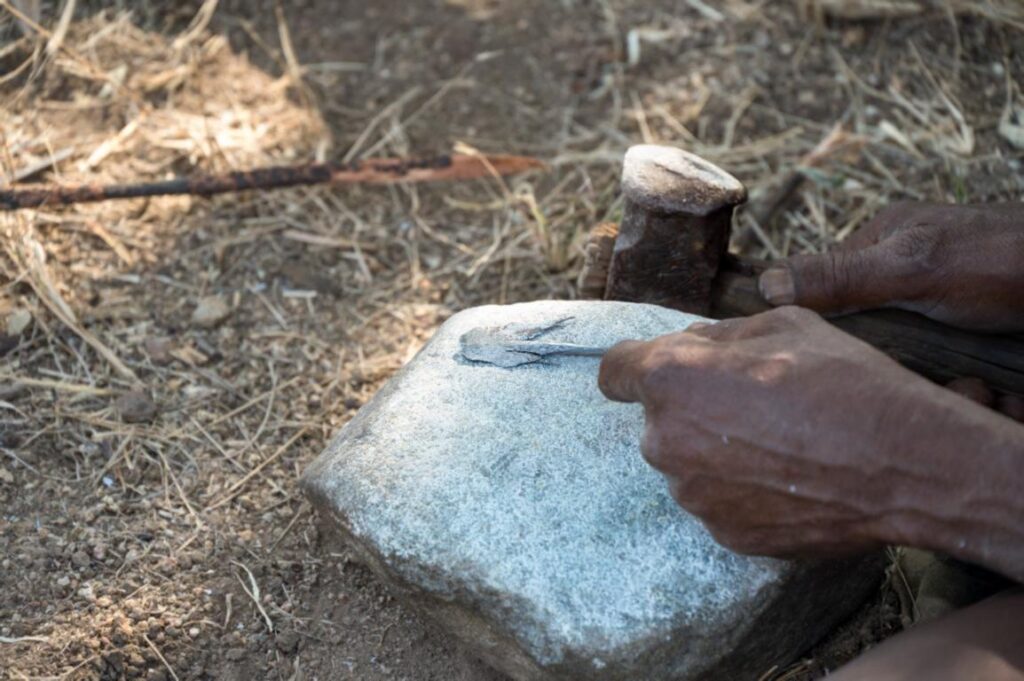
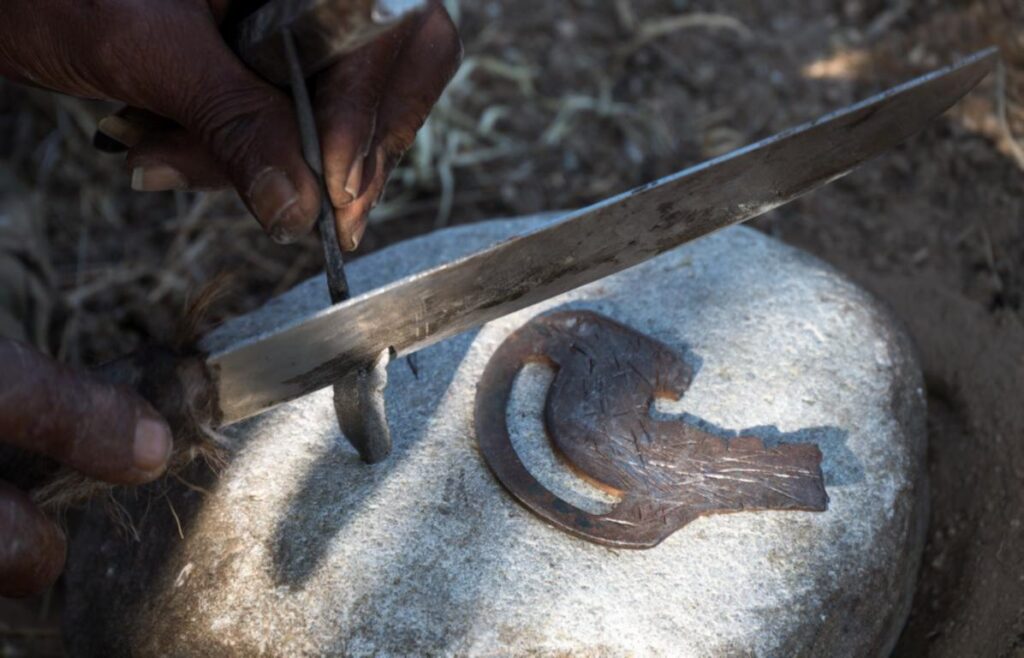
Thereafter, he uniformly widens the gap of the barbs on both sides. He uses his hunting knife to hammer down the gaps.
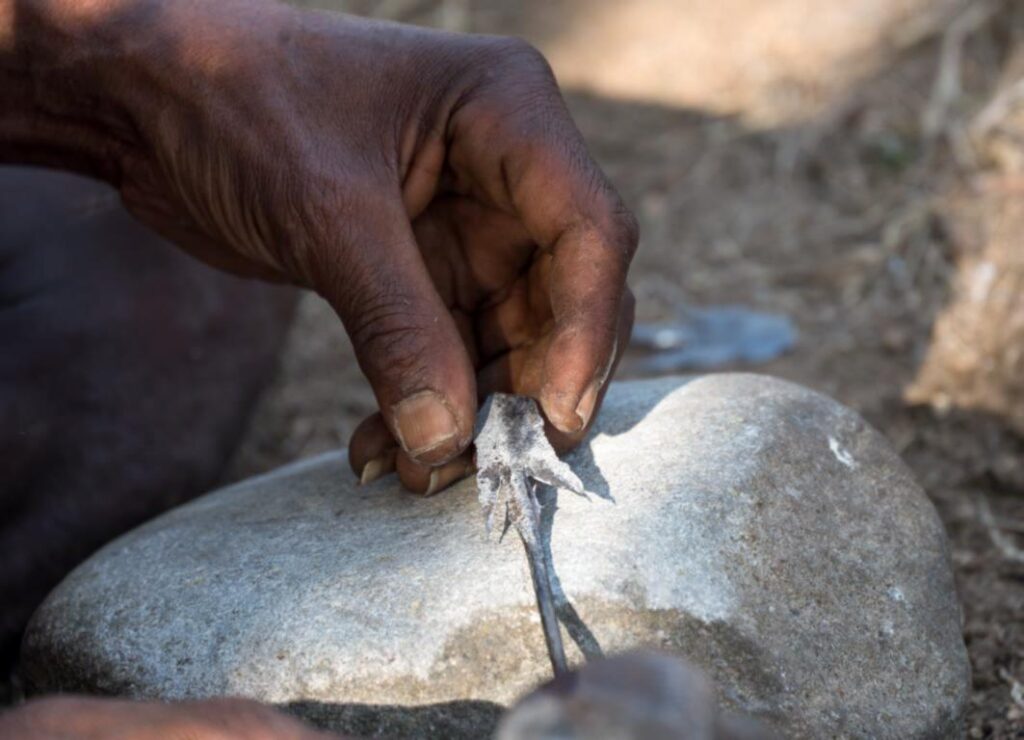
After the head is flat enough and the barbs’ gaps are at the right angle, he will cold-chisel the final shape of the iron arrowhead.
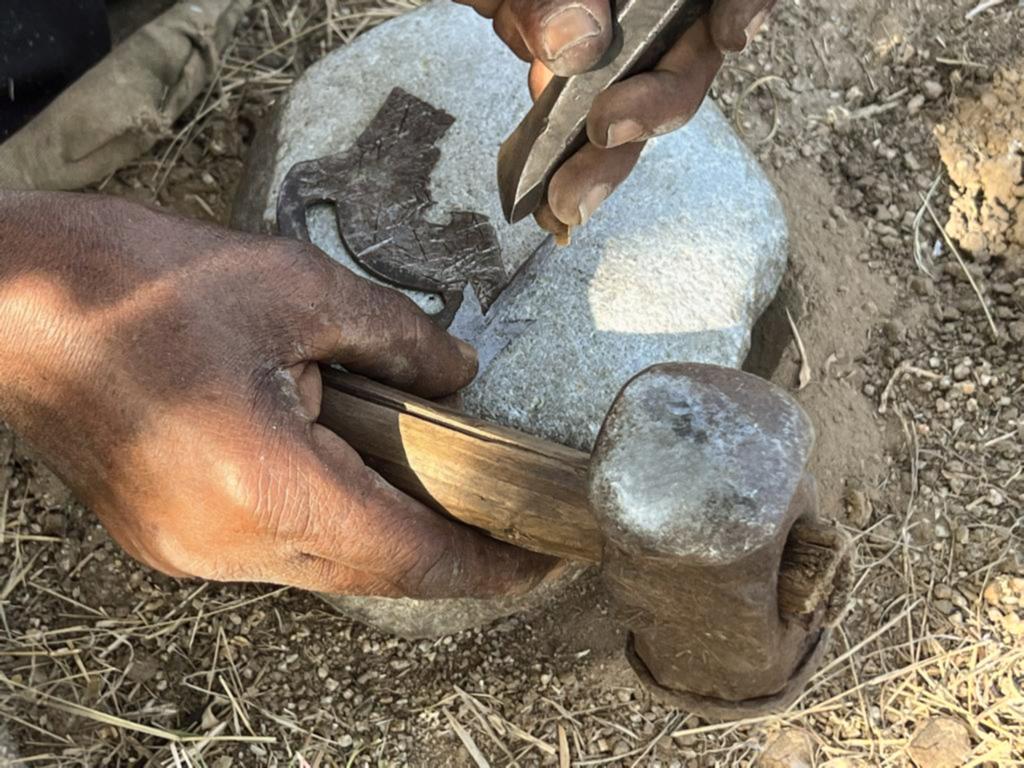
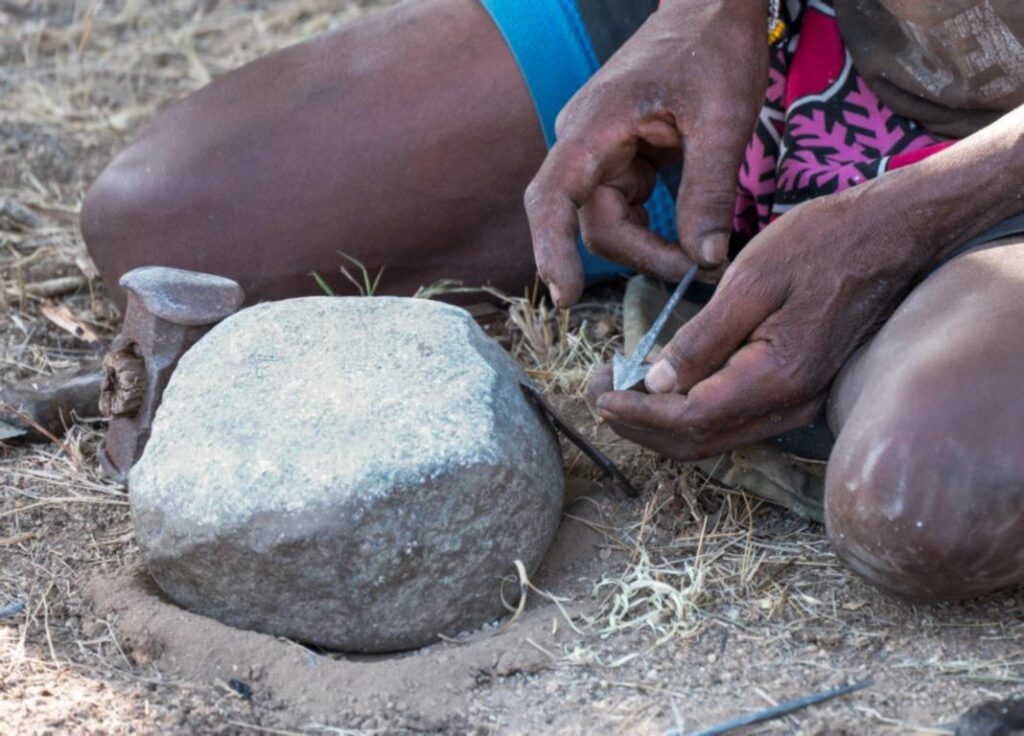
Although the tools used are very rough and rudimentary, surprisingly, even-shaped iron arrowheads are produced with this method. As they can’t sharpen the cold chisel, the edges of the broadheads are rather shaggy. However, this does not limit their value on the targets, as they cut and act like saw teeth on skins and meat.
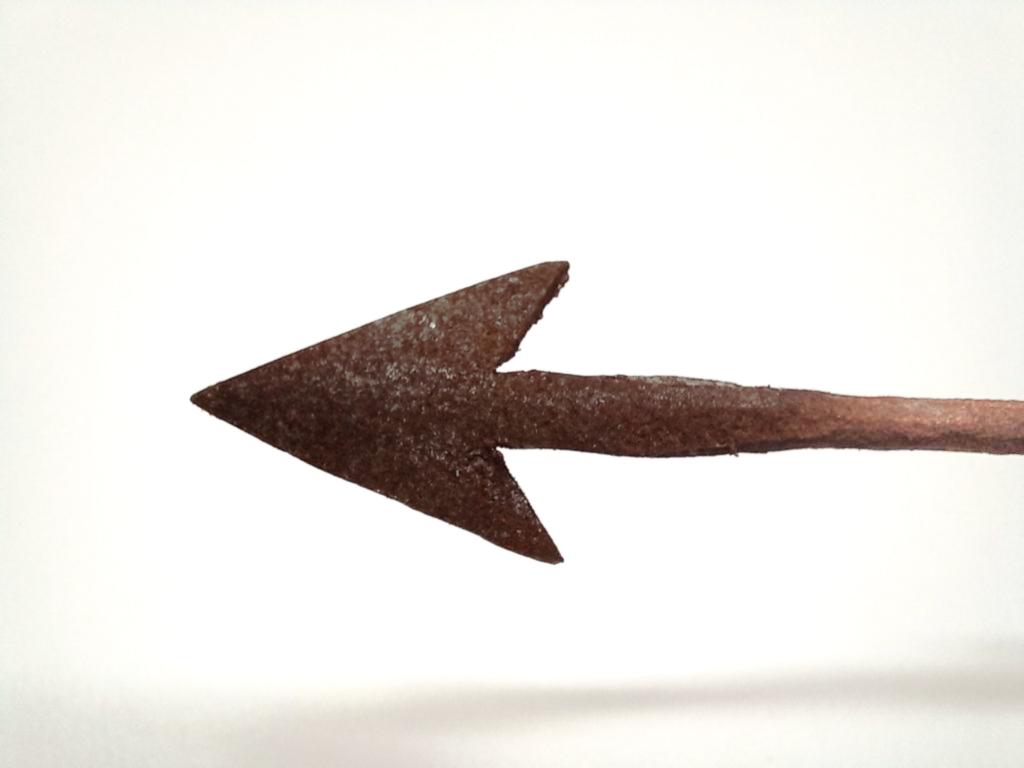
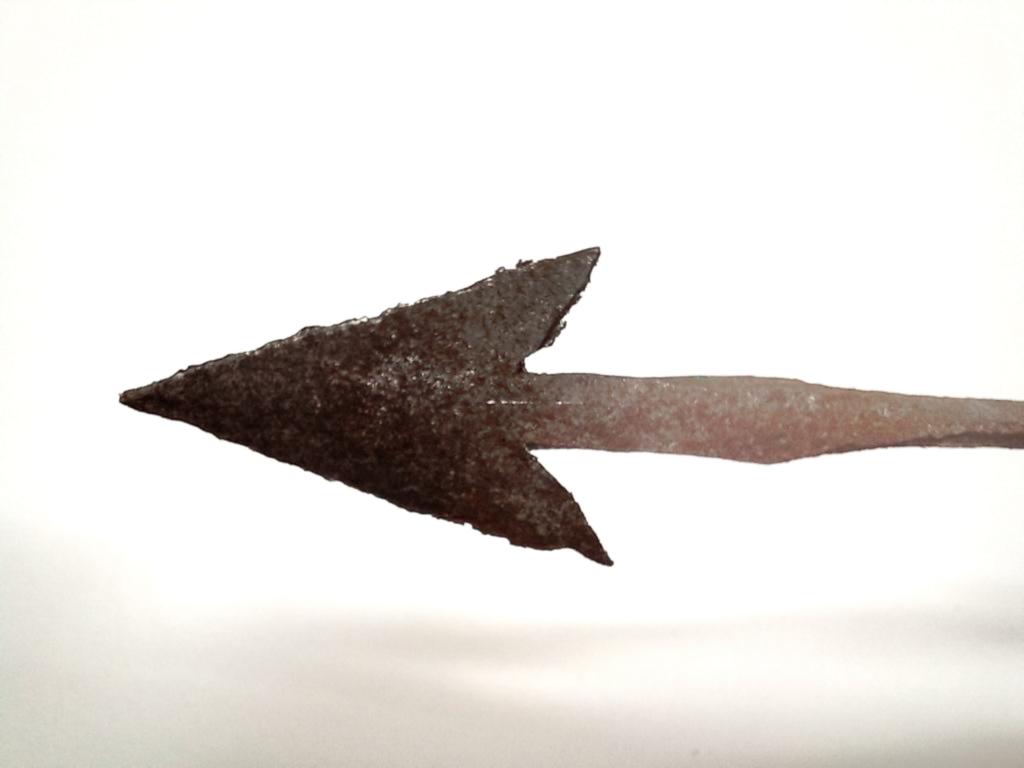
Fitting the arrowhead into the shaft
One of my previous articles on this website already discussed preparing the arrow shafts. Initially, the finished arrowhead is held upside down between both heels. The arrow shaft will be drilled into the conical end of the head using the same motion as friction fire lighting.
Within a minute, the iron shank is drilled deep enough into the arrow shaft to hold there securely.
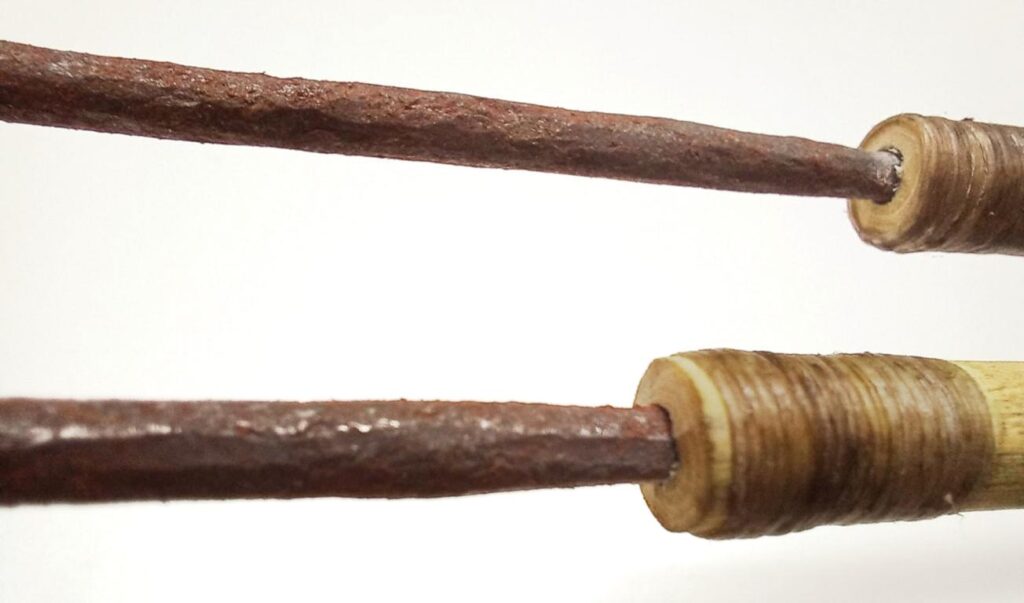
As a final step, ligaments will be wrapped around the connection area to prevent the shaft from splitting. These are the materials already discussed in connection with the arrow fledgings.
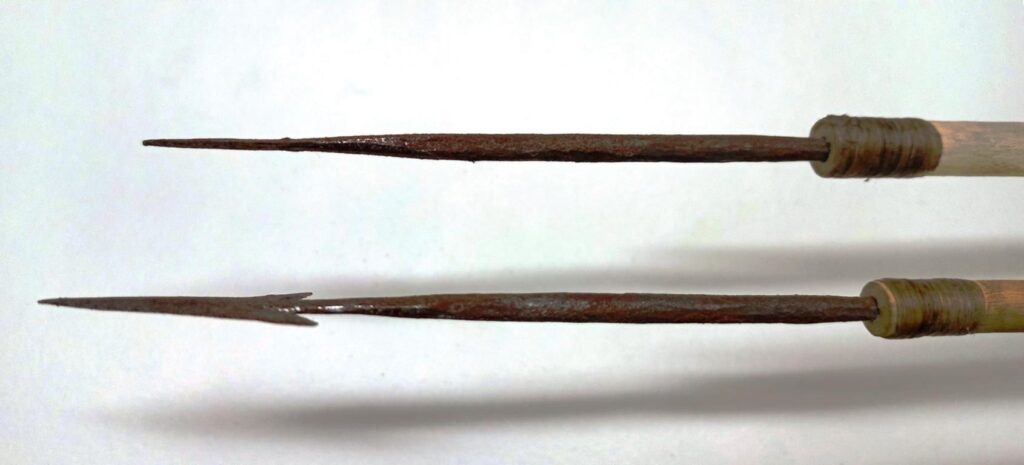
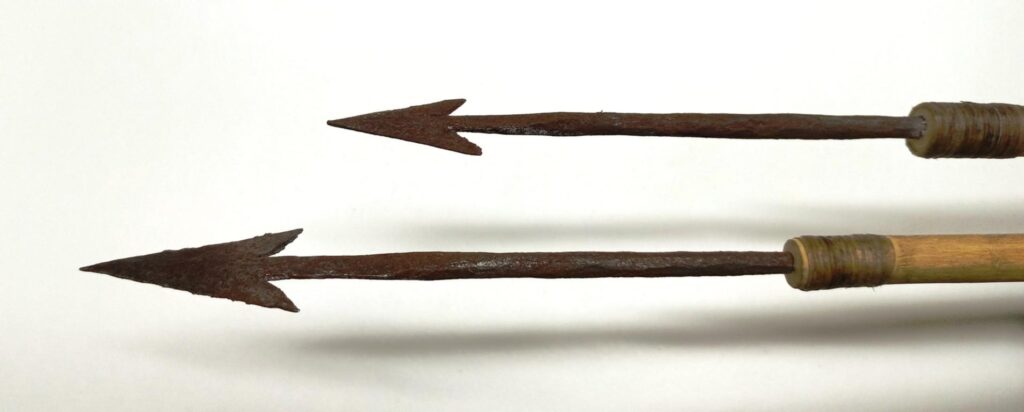
Lessons learned from cold-forging of iron arrowheads:
- The Hadzabe people use heavy framing nails to cold-forge the iron arrowheads
- From each nail, two arrowheads can be produced.
- Production is done in three stages by three people, all using the same iron hammer, chisel, and anvil stone.
- In addition to the above-mentioned tools, they also need a scrap metal plate as a counter-base for fine-crafting the flat broadhead shape.
Additional information
My book ‘Hadzabe Survival Skills‘ offers more skills, knowledge, tools, and techniques for the Hadzabe people’s life in their natural environment. It is available on Amazon.com and Amazon’s regional websites.
.